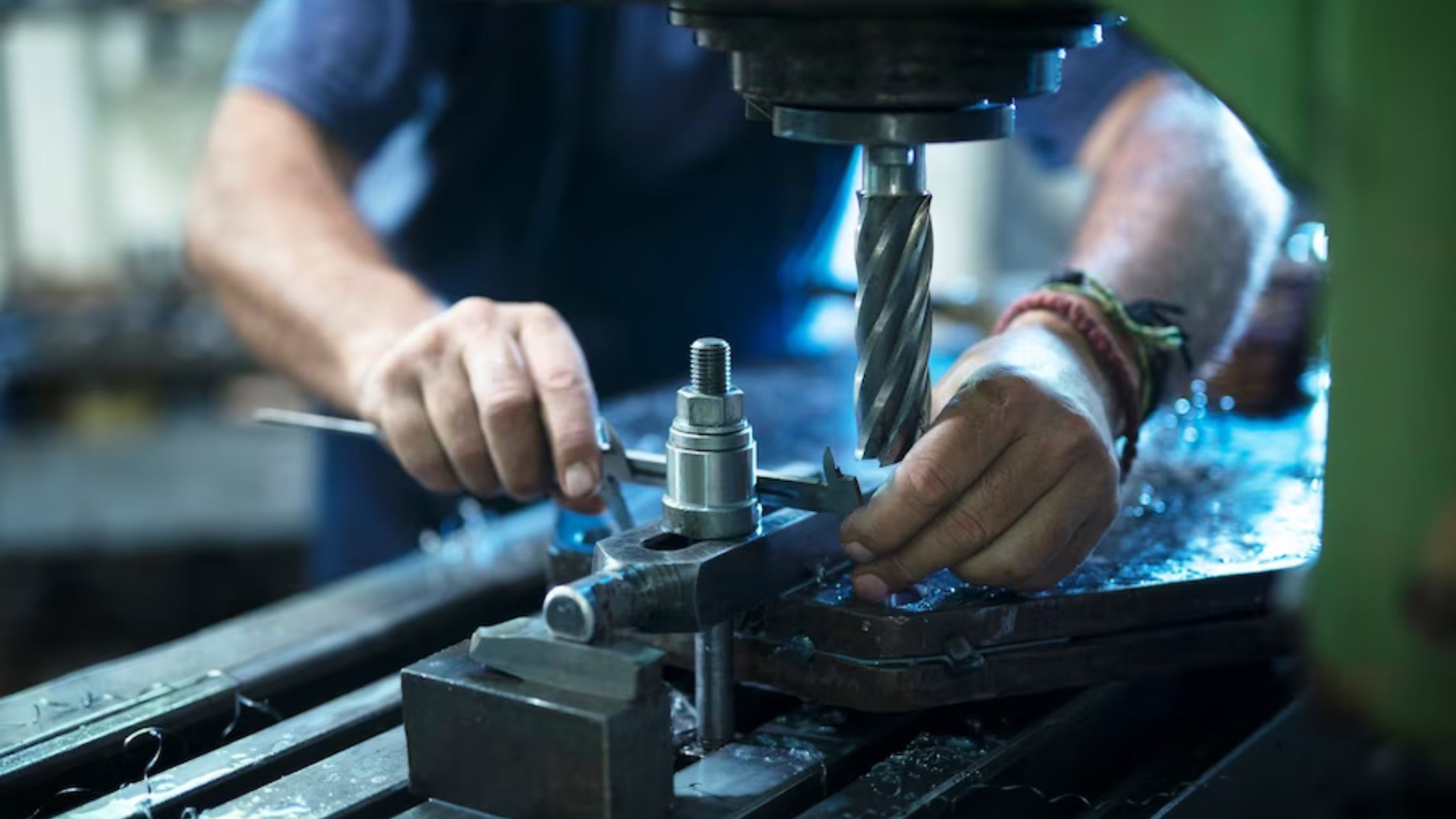
A Comprehensive Guide to CNC Machining for Beginners
CNC machines are the best standard in term of manufacturing as it is known for their speed, precision, and capacity to hold tight. The CNC machine has developed in the last few years and has incredible facilities. The innovative features make it the best at manufacturing complex geometric parts and intricate designs.
The CNC stands for Computer Numerical Control, a machining process pre-programmed in computer software to facilitate the movement of machines and tools. With this rapid CNC machining process, three-dimensional cutting can be done easily.
So, if you want to use CNC machining to produce your products, you should understand it better. Let’s look at the overview, types, benefits, and limitations.
Table of Contents
What does CNC Machining mean?
CNC is a Computer numerical control that is a kind of machining process mainly controlled and regulated by a computer. The computer system allows the machining to manufacture products even more faster, accurately, and precisely.
CNC machining helps in producing more complex geometric designs in a better way as compared to other manual machining. It reduces manual machine labor. But there are certain works that are done by humans to ensure the proper and smooth functioning of the machines.
How does CNC Machining work?
The programs are input into the CNC machining written in G-code created by CAM (Computer-aided manufacturing) software. This G-code is for 3D models with numerous intriguing tools and materials.
When the CNC machine is turned on, the designs are programmed into software, and the tools start making those specified dimensional tasks precisely. The tools placements in the numerical control system are done by a series of inputs which is called the part program.
These inputs allow tools to get placed as specified to give out the best results. Moreover, G-code also commands to turn on or off the coolant and other components of the machine. CNC machining is widely used in varieties like aluminum, brass, Delrin, nylon, ABS, etc.
Types of CNC Machining
The most common types of CNC machining are electronic and are used in ultrasonic welding, laser cutting, and hole punching. Following are some common types of CNC machining:
CNC Milling
Milling is the most popular CNC machine that uses integrated tools for drilling and cutting. Materials are put inside the milling CNC machine, and then the program is coded, instructing the machine to cut or drill them as specified.
They are mostly available in 3- to 6-axis settings used to manufacture spur gears or make slots in the bore.
CNC Turning
The materials are chucked and rotated in this machining to get desired designs. This machine shifts the raw material bar and clears them to create intricate designs; it is also known as subtraction machining.
CNC Grinding
It is a type of cnc precision manufacturing machining. It works on rotating wheels cutting metal into ball bearings, transmission shafts, and camshafts. It offers high accuracy and precise production.
CNC Lathes
Workpieces are cut down in circular motion with high precision and velocity in this machining. It is used to produce complex designs that cannot be manually done.
CNC Drilling
This machine is usually applied when mass production is required. This CNC machining has multi-function features that make it ideal for performing different operations like creating holes, reaming, counterboring, etc.
Benefits of CNC Machining
A few important benefits of CNC Machining are:
- High accuracy and precise design that ensures consistent product quality.
- Excellent production speed and efficiency of CNC manufacturing.
- Highly intricate designs can be created, and mass production can be done.
Limitations of CNC Machining
Following are some points that make CNC machining less compatible with others.
- CNC manufacturing is very expensive than manual manufacturing.
- The tools and coding is used, which are costly to buy and hire.
- It required highly skilled individuals and talented programmers to pass and operate code into the machine.
Tips for reducing CNC cost
Following are some important tips for cost reduction:
- Limit the use of tight tolerance (±125)
- Keep the depth of products at four times its length.
- Create thick walls instead of thin, as thin walls are fragile and will cost more in operation and maintenance.
- Adjust the design of parts to create rounded corners. This way, your machine will run for a long time compared to the sharp-edge designs.
- Make use of standard-size drills rather than using custom sizes. It will optimize manufacturing operations.
Key takeaways
If you are planning to get started with CNC manufacturing services, know all the points mentioned above. It will increase your production speed and will deliver the best quality products. You must consider some of the cost optimization tips to make high profits.
To get detailed CNC products with intricate designs, utilize the most efficient and cost-effective tools like wood routers, foam cutters, 3D printers, glass cutters, wire-bending machines, etc. Get amazing performance with CNC and thrive in the manufacturing industry with your machining.
August 11, 2023