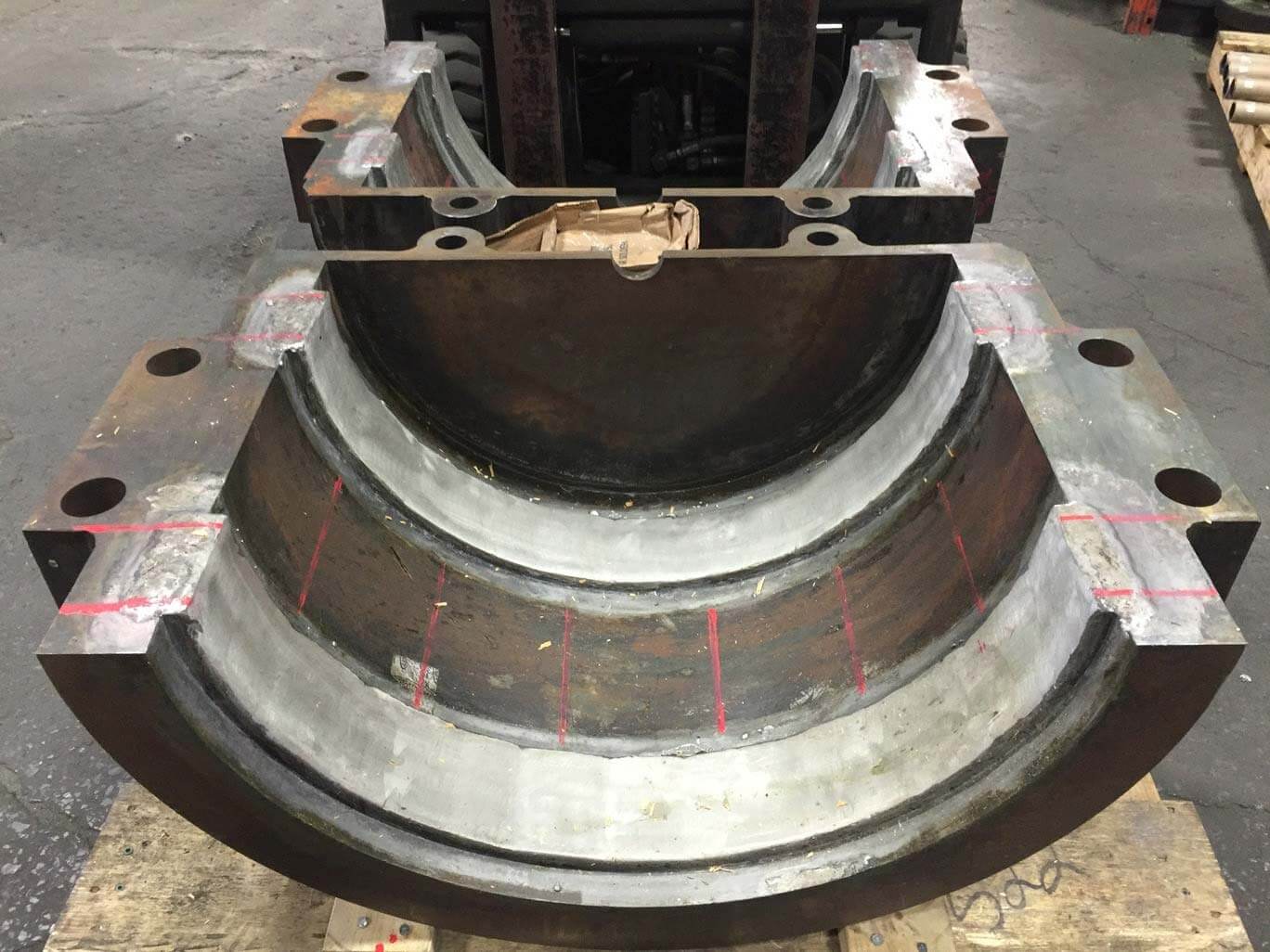
How To Pour Babbitt Bearings
Using Babbitt bearings in an engine is a time-tested and historical way to protect the parts from wear and tear. They work hard to support the mechanical parts in the engine that move so that they aren’t torn down by frictional degradation. However, it may be difficult to find these bearings commercially, so you’ll have to do your own Babbitt bearing repair.
What is a Babbitt Bearing?
Babbitt is a combination of both tin and lead, and it is normally 80 ¼ percent lead, 14 ¾ percent antimony, and 5 percent tin. This makes for an incredibly durable bearing that can last for years as long as it is well oiled and doesn’t run hot. Salvaging the bearing that already exists in the engine is a great way to save yourself the trouble of looking for commercial Babbitts and create a product that you know will last a while.
Don’t worry about the grime, dirt, oil, and grease that covers the bearing when you pull it out. All of that will burn off during the babbitting process. There are numerous ways to remove it from the molten Babbitt, including using a plumber’s soldering iron or another piece of flat steel or by using small bits of wax from a toilet bowl ring.
Of course, if you’re worried about the age of the Babbitts and don’t think that the babbitting process will get rid of all the impurities, you may consider making your own. This will involve getting the raw materials and melting them down to form the new bearings. More in-depth instructions are below.
The Babbitting Process
To begin the process, you must have a way to melt the babbitt. Using a rosebud torch or oxy-acetylene torch could be helpful. It may also be possible to use a white gas plumber’s stove. It all depends on what you have at your disposal. You will also need a variety of pots and ladles for melting the babbitt. These are often constructed of cast iron so that it can handle the extreme temperature of the melting process.
Once the metal has reached the desired temperature, you’ll need to remove any impurities that may have risen to the top. Again, this can be done with a flat piece of metal or the wax from the toilet bowl ring.
Then, the molten metal can be poured into the bearing shell. Having a ladle with a spout on one side will make this process much easier.
The bearing will need to be fully cooled before working with it. Using a drill, you can form the drill holes in the bearing, making sure to get rid of the excess metal that appears after drilling. Don’t forget to add the oil groove while conducting Babbitt bearing repair.
Finding Babbitt bearing repair services may not be an easy task. However, there’s nothing stopping you from doing your own. Talk to the professionals to get all the supplies you need to fix your own.
August 1, 2019